解决粘弹体防腐胶带施工过程中的气泡问题至关重要,因为气泡会形成空腔,成为水分和腐蚀介质侵入的通道,严重降低防腐效果和胶带的自修复性能。造成粘弹体防腐胶带贴服不实,出现气泡的原因主要有基材处理不当、施工操作问题、环境因素和材料缺陷等
一、气泡产生的原因
1. 基材处理不当:表面残留油污水分锈迹或灰尘,会导致粘弹体胶带与基材粘附不牢出现气泡。
2. 施工工艺问题:胶带缠绕时张力不均、搭接不紧密或未充分按压,或胶带拉伸过度或回弹不足,容易形成内部空隙。
3. 环境因素:不当的高温或低温导致胶带粘弹性变化,影响贴合性;湿度过高会使水汽滞留产生气泡。
4. 材料缺陷:胶带本身存在质量瑕疵,比如局部脱胶或有结块厚度不均,都可能导致胶带起泡。
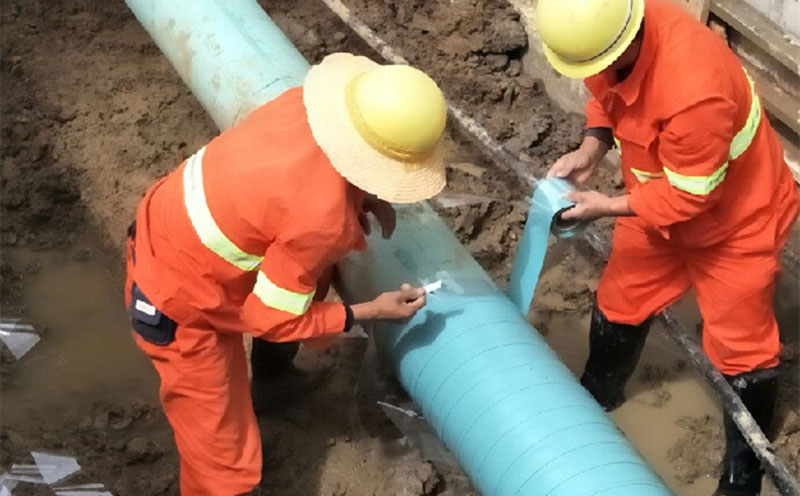
二、气泡预防与解决方法
1. 基材处理
彻底清洁: 使用适当的溶剂清除油脂灰尘和污垢等残留物,确保表面达到清洁度标准。
完全干燥: 表面必须绝对干燥,任何残留水分在胶带覆盖后受热都可能汽化形成气泡。施工前和施工中要确保环境湿度低于要求,必要时用干布擦拭或热风枪吹干。
温度适宜: 确保基材表面温度高于露点温度至少3°C,并符合胶带施工的温度要求,低温会降低粘性,增加气泡风险。
光滑处理: 对于焊缝、毛刺、尖锐边缘等,必须打磨光滑(R<2mm),对管道表面的凹坑、裂缝等缺陷,用专用修补剂或腻子填补平整,避免形成空隙或刺破胶带。
2. 规范缠绕施工
适度拉伸: 大多数粘弹体胶带需要均匀、适度的拉伸,拉伸不足会导致褶皱和层间空气;过度拉伸会减薄胶带、降低弹性恢复力并产生过大内应力,后期易形成气泡或脱胶。缠绕时要保持持续、均匀的张力,松紧适度。
紧密搭接: 胶带缠绕是要紧密,并确保胶带有足够的搭接宽度(通常50%-55%),用力压紧搭接边缘。
缓慢施工: 缠绕速度不宜过快,给胶带足够的时间在压力下流动并贴合基材表面,排出空气。特别是在复杂形状或焊缝处更要慢速操作。
滚压排气: 在缠绕每一圈/每一段胶带后,立即使用硬质橡胶滚轮(带花纹或凸点的更佳)或尼龙刮板,从中心向两侧(或从缠绕方向的下方开始向上)用力滚压。
全面覆盖: 确保滚压覆盖整个胶带表面,特别是搭接缝、焊缝、凹陷处、弯头、三通等复杂部位。滚压要施加足够的压力,使胶带与基材和自身层间紧密贴合。对于关键部位或较厚的缠绕层,进行多次滚压,确保空气完全排出。
处理异形件: 对于法兰、阀门、弯头、三通等,采用正确的缠绕方法(如"8"字型、剪切法),并加倍滚压,必要时使用小块胶带预先填充凹陷处。
3. 环境控制
温度: 确保环境温度和基材温度在胶带要求的施工范围内,温度过低时胶带变硬,粘性和流动性都会下降,会增加排气的难度,必要时可以用热风枪加热基材和胶带。
湿度: 避免在雨雪、大雾或高湿度(RH>85%)环境下施工。湿度高时,即使基材干燥,空气中的水汽也可能在胶带和基材间冷凝。
搭建工棚: 在寒冷或风大环境下施工,搭建防风保温棚。
4. 气泡修复
直径<5mm小气泡用滚轮或刮板从边缘向中心挤压排气,使胶带重新贴合,必要时局部补胶。大气泡则切开气泡处将空气彻底挤出,然后用力滚压切口区域使其闭合。对于非常大的气泡或无法有效修复的区域,必须割除该部分胶带,重新清洁表面并修补。
解决气泡问题的核心在于清洁基材、规范施工、环境适配,关键是我们要选用正规厂家生产的粘弹体胶带,注意检查胶层均匀性、无脱胶或结块;施工时使用与胶带宽度匹配的滚轮,操作人员需掌握胶带拉伸率、搭接比例等参数,规范施工;施工后24小时内复查,温度变化可能导致二次气泡(尤其昼夜温差大时)。通过科学的工艺控制与细节管理,可将气泡率降至1%以下,确保粘弹体防腐胶带的长期密封性和防护效果。